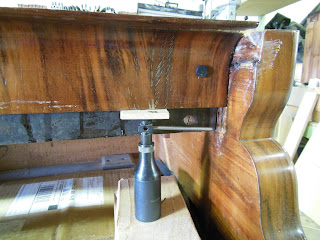
Here is a front view of the stretcher fascia, being slowly jacked up and out of the instrument. Behind it you can see the iron bar, which is actually quite large and heavy, and is secured by a somewhat motley assortment of screws, in an odd arrangement. Above, the iron bar revealed. This is sort of like putting the pin-block flange, behind the pin-block. Erard was not the only one to do this. the remaining plate strut projects all the way through the stretcher and contacts the bar, without actually being attached to it. A closeup of one end of the iron bar, showing also the groove into which the spline of the fascia fit. This groove is about 1/8" deep, and is cut just through the veneer, which is very thick in this area. The name stamped on the back of the bar (CHATILLON.SS)